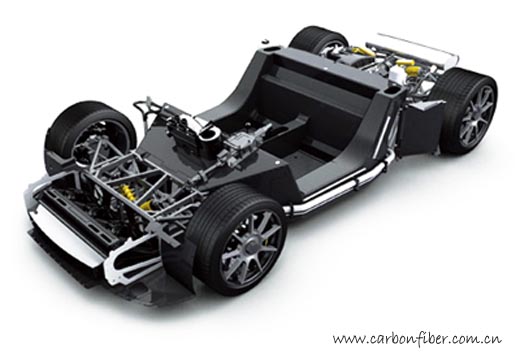
圖1 安裝在底盤上的碳纖維復合材料主承載結構
在汽車工業發達國家,一些小批量生產的高檔汽車及賽車已使用了采用碳纖維增強環氧樹脂復合材料制成的主承力結構件,其強度、剛性及其他各項性能指標均可與傳統的金屬材料部件相媲美,同時重量也大為減輕。本文主要從材料和加工工藝等方面對此進行闡述。
自20世紀70年代第一次石油危機爆發以來,“汽車輕量化”便成為全球汽車制造業關注的重點之一。幾十年來,人們不斷地通過優化結構設計以及采用金屬替代方案來實現減重的目標。近年來,隨著工程塑料及復合材料等非金屬材料在汽車內飾、外飾及功能件應用方面的日趨成熟,替代金屬將它們用作結構件正成為汽車制造業新的研究課題。這其中,尤其以汽車主承力結構件(簡稱“主結構件“)的輕量化為制造研究的重點和難點。 copyright 123456
近些年來,隨著長纖維增強復合材料(LFT)和片狀模復合材料(SMC)及其加工技術的快速發展,國內外已出現了由這類材料經模壓工藝制成的零部件,如車門骨架、發動機托架、座椅骨架及散熱器支架等。然而,由于材料本身的限制,其強度、剛性及抗沖擊性等均不能滿足結構件特別是主結構件的要求。
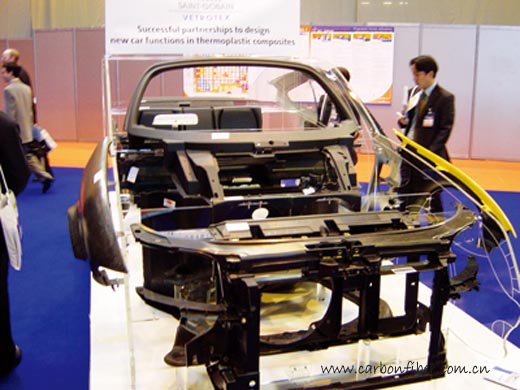
圖2 在2005年JEC展會中展出的復合材料車身結構
主結構件,包括汽車的A、B、C柱,以及由翼子板、前圍、側圍、后圍、頂梁和底板等構成的車身框架。由于是汽車的主要承載部件,為了確保足夠的安全性能,汽車廠商會選擇強度、剛性及耐沖擊性能均很高的材料,通常是復合材料層合結構。相比之下,次承力結構件,包括車門、發罩、行李艙門和頂板等,它們通常使用的是復合材料三明治夾心結構(包括蜂窩夾心、泡沫夾心和輕木夾心等芯材)和層和結構。在此,暫不對三明治夾心結構進行表述,主要介紹復合材料實體層合結構。
copyright 123456
在汽車工業發達國家,一些小批量生產的高檔汽車及賽車已陸續使用了碳纖增強環氧樹脂復合材料制成的主結構件和次承力結構件,其強度、剛性、抗疲勞性及其他各項性能指標均可滿足設計要求,可與傳統的金屬材料部件相媲美。此外,此類產品還表現出了極好的抗腐蝕和耐腐蝕性能。與同體積的鋁合金構件相比,減重可達50%。下面將從材料、加工工藝等方面對此進行詳細闡述。
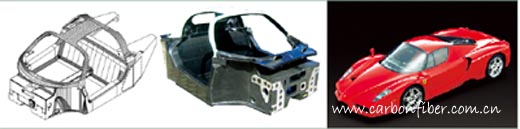
圖3 Ferrari Enzo 復合材料車身
碳纖維增強環氧樹脂復合材料
作為一種設計靈活、輕質、高強、耐沖擊及耐腐蝕的材料,環氧樹脂基復合材料可用于制造多種汽車部件。除了車頂棚、門外板、翼子板以及發動機罩等車身部件外,它還可用于汽車主結構件。由此類材料制成的汽車部件不僅大大提高了汽車的安全性能,而且還降低了車重,減少了燃油消耗,提高了經濟性,另外改善了美觀性,如為車身帶來碳纖維的外觀效果。
123,123
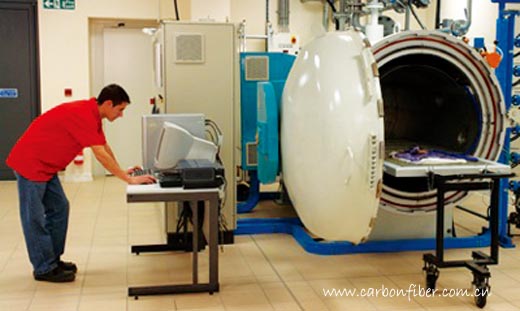
圖4 制袋完畢,進入熱壓罐加熱加壓固化
根據應用的不同,增強材料可選用玻璃纖維、碳纖維及芳綸纖維,甚至硼纖維等。對于主結構件而言,由碳纖維、芳綸纖維或硼纖維增強的環氧樹脂基復合材料能夠提供更高的強度和剛性,因此成為主結構件的首選材料。近年來,國外一些高檔汽車如奔馳、寶馬、保時捷和蓮花等,以及世界上的幾大賽車品牌,如法拉利、瑪莎拉蒂、蘭博基尼和波爾舍等,均已采用了由碳纖增強環氧樹脂復合材料制成的主結構部件。此外,F1方程式賽車還全部采用了碳纖和硼纖維增強環氧樹脂復合材料制成的車身。一般,碳纖增強環氧樹脂復合材料中的纖維含量在60%~70%左右。與玻纖增強的環氧樹脂相比,其密度更低、質量更輕、剛性更好且質感更加美觀;與金屬材料相比,其強度更優,抗疲勞性能更佳。不僅如此,根據應用要求,還可對碳纖增強環氧樹脂進行局部或整體增韌處理,即通過加入一些熱塑性樹脂,如PEEK和PEKK等,提高材料的耐沖擊性能,使其可提供更好的安全性能。由于具有優異的綜合性能優勢,目前碳纖增強環氧樹脂復合材料已被大量用于飛機的主承力結構和次承力結構中,最新研制的波音787商用飛機所使用的復合材料量已占到飛機總質量的50%。
123456
碳纖維增強環氧樹脂復合材料主結構件的加工工藝
眾所周知,熱固性復合材料的可設計自由度非常大。在制件的生產過程中,完全可以根據制品的最終使用性能要求,選擇不同的纖維和基體樹脂,然后按照不同的方向和厚度完成纖維的鋪層。然而,由于此類材料的生產工藝目前仍以手工操作為主,機械化程度不高,因此很少能實現量產。
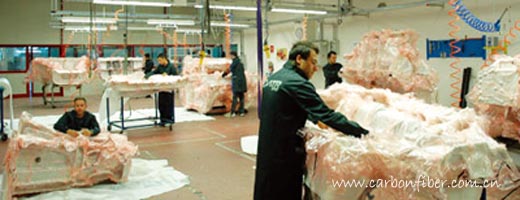
圖5 采用預浸料/熱壓罐工藝的生產現場
目前常用的熱固性復合材料制件的生產工藝主要包括:手糊成型,手糊袋壓成型(Hand lay-up with bagging film),噴射成型,纏繞、拉擠成型,樹脂傳遞模塑成型(Resin transfer molding,簡稱“RTM”),樹脂膠膜浸潤成型(Resin film infusion,簡稱“RFI”)以及預浸料/熱壓罐成型和模壓成型等。對于制作汽車主結構件而言,適合的生產工藝主要為手糊袋壓成型、RTM、RFI以及預浸料/熱壓罐成型等。至于手糊成型,由于生產出的部件孔隙率較高,其強度達不到主結構件的要求,因此一般不予采用。目前,只有RTM、RFI和預浸料/熱壓罐成型是可以量產的生產工藝。
copyright 123456
1、手糊袋壓成型
與普通的手糊成型相類似,手糊袋壓成型也是由手工將樹脂和纖維織物交替地鋪層在已涂有脫模劑的模具上,使其達到設計厚度要求。所不同的是,在進行加熱加壓前需要先制袋,制袋的目的是為了在鋪層間形成真空并達到一定的接觸壓力,以降低最終制件的孔隙率,同時提高層間剪切強度。制袋完成后,即可將其放入熱壓罐或固化爐中,經加熱加壓后成型。這種工藝方法勞動強度大,生產周期長,工作環境差,但成本低,目前很少被用于主結構件的制造中。
2、樹脂傳遞模塑成型
樹脂傳遞模塑成型(RTM)是一種閉模成型工藝,對于要求雙面光滑且形狀復雜的部件較為適合,汽車的A、B、C柱以及翼子板等部件可采用該成型工藝。其特點是,先按設計要求在模具型腔中放置增強材料預成型體,然后合模加壓,從澆口處向型腔中灌注預先計量好的定量液態樹脂,使其充滿纖維預成型體的纖維間空隙,經加熱固化后成型。當模具本身帶有加熱功能時,加熱固化過程可直接在模具中完成,否則可使用固化爐完成此過程。該工藝可使用的纖維增強材料包括兩種類型,一種為手工鋪貼纖維,另一種是經過三維編織的預成型纖維。
copyright 123456
為了確保主結構件獲得更高的強度和質量,還可采用真空輔助的RTM工藝(簡稱“VARTM”)。該工藝是在合模后,先對型腔抽真空,然后再灌注樹脂,這樣可以有效地排除型腔中的空氣,從而降低制品的孔隙率以提高強度。
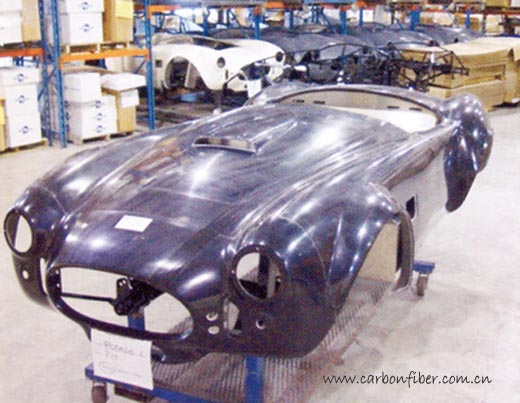
圖6 采用RFI工藝制作的車身
需要說明的是,由于樹脂是在閉模狀態下被灌注到型腔中的,壓力越大,樹脂的浸潤性就越好,可保證樹脂可以充滿整個型腔。因此,RTM工藝對模具的要求相對較高,要求模具要具有較高的強度,以承受極高的壓力和溫度。例如,當固化溫度為180℃時,要求模具必須能夠耐受200℃的高溫,同時要能夠承受3~4kg/cm2的壓力。當然這是指用于生產數量較少的非金屬模具而言,對于批量較大的零件,通常采用金屬模具。不僅如此,模具的澆口和冒口位置的選取和設計也非常關鍵,一般需要憑經驗,或在電腦上進行仿真模擬,否則會出現“干區”或“貧膠”現象。除了需要使用RTM注射機等專用設備外,RTM工藝一般不需使用熱壓罐,因而其設備成本相對較低。總之,采用RTM工藝生產的制品具有較高的力學強度和良好的表面質量和較高的尺寸精度,與手糊袋壓成型相比,其生產效率較高。
內容來自123456
3、預浸料/熱壓罐成型與樹脂膠膜浸潤成型
無論是手糊袋壓成型還是樹脂傳遞模塑成型,鋪層是一件費時費力的事情,要求技工要富有經驗且手藝嫻熟。正因如此,使得這兩種工藝生產效率低下,不能滿足較高的量產需求。
為了解決這一問題,目前一些材料供應商開發出了所謂的“預浸料”。這是一種樹脂與纖維預混好的半固化態材料,即纖維預先經過樹脂浸潤,并將被樹脂浸潤過的纖維鋪放到特殊載體上,形成布狀或帶狀預浸料,甚至絲狀預浸料。其工藝特點是,逐層鋪貼預浸料于模具上,形成零件疊層,然后經熱壓罐加壓加熱固化成型。使用該材料時,在操作過程中不易出現纖維的滑動和彎曲現象,纖維方向的一致性和準直度可以得到較好的控制。此外,在熱壓罐壓力的作用下,可以實現較高的纖維含量,故可以得到較高的力學性能。
copyright 123456
由于使用半成品的預浸料,可以連續鋪貼,提高了速度,因而取代了以往重復交替的纖維和樹脂的逐層鋪貼工序,使得生產效率大為提高,成為一種普遍采用的量產化的生產工藝。根據制品的不同,預浸料成型工藝的產量一般在幾千到幾萬件之間,非常適合于定制產品的生產。
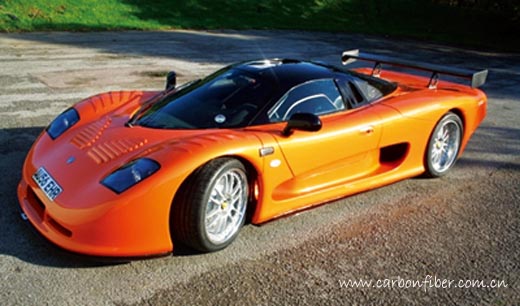
圖7 Mosler MT900S全復材車身
一般情況下,預浸料成卷狀供應。為了防止受熱后失效,通常需要將其放置在-18℃的低溫環境中保存。使用時,先對其解凍,然后按照電腦上排序好的零件展開圖切割下料,其切割可由機器完成。下料后,根據鋪層設計、按施工工藝要求在模具上進行手工逐層鋪貼。接著進行制袋,以使其內部處于真空狀態并產生負壓,最終消除成型過程中的孔隙率。制袋完成后,將其送入熱壓罐或固化爐中,在170~180℃的溫度下,6~8h即固化成型。
copyright 123456
預浸料/熱壓罐成型工藝的優點是:施工簡便,對工人的技能要求不高,生產效率高,制品質量穩定且強度高,因此,該工藝已成為汽車結構件的主流生產技術。需要說明的是,在熱壓罐中固化成型的制品與在固化爐中成型的制品相比,其致密性更高。這是因為熱壓罐可同時加熱加壓,其施加的壓力通常為2~3個大氣壓,而固化爐則不能施壓,這使得在熱壓罐中成型的制品具有更高的致密度,其強度性能更好,因而更適合于主結構件的成型。對于次結構件而言,固化爐成型完全可滿足其強度和質量要求。當然,熱壓罐的成本幾乎為固化爐的2~3倍。
盡管預浸料/熱壓罐成型工藝能進一步提高制品的強度和質量,同時能實現量產化,但其昂貴的材料及設備成本卻使得汽車廠商望而卻步,目前也只有一些高檔汽車和賽車的結構件采用這種成型工藝。
copyright 123456
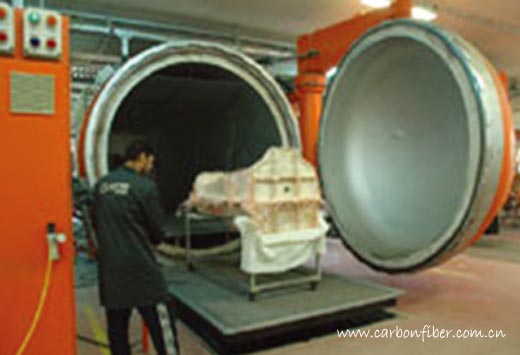
圖8 鋪貼制袋完畢的零件準備進熱壓罐固化
為了降低成本,可以用樹脂膠膜浸潤成型(RFI)工藝取代預浸料成型工藝。該工藝是在干纖維的下面鋪放膠膜,并將零件和模具包覆于真空袋中,在熱壓罐內完成固化成型。在固化過程中,隨著溫度的升高,膠膜熔化,在壓力和真空的作用下,樹脂浸潤分散到纖維內部空隙固化成型。與預浸料/熱壓罐工藝類似,RFI工藝施工方便,不需要高技能的操作人員,并且制品的質量穩定、強度高。由于該工藝不使用預浸料,因而材料成本相對降低,并可對纖維進行縫編處理,加強了零件方向上的強度,對大型制件有一定益處。當制品需要雙面光時,還可采用閉模熱壓成型的方式。
主要的碳纖維材料供應商
由于制造工藝復雜,目前碳纖維制造技術主要集中在全球少數幾家廠商手中,并且每家廠商所采用的工藝也不盡相同。另外隨著航空市場的發展,在產能沒有增加的情況下,使得全球的小絲束碳纖維需求相對緊張。目前全球可提供小絲束碳纖維的公司主要有:日本的東麗(Toray)公司、東邦(Toho)公司和三菱(Mesitsubishi)公司,美國的Cytec公司和Hexcel公司,以及臺灣的臺塑。其中日本3家公司的產量占全球產量的85%,其產品品級涉及航空級、工業級和建筑級。美國Cytec公司只提供航空級的產品,除此之外,Cytec還提供碳纖維增強環氧樹脂預浸料。該公司的預浸料包括兩種固化溫度等級,一種為121℃,另一種為177℃。需要說明的是,隨著固化溫度的提高,材料的強度也就越好,同時其價格也更加昂貴。
內容來自123456
基于碳纖維優越的綜合性能優勢,除航空和汽車工業外,建筑及其他許多工業領域也已開始關注這種材料。隨著需求的日益增大,有限的產能導致碳纖維材料的價格一直居高不下,從而阻礙了其在汽車零部件特別是在汽車結構件應用領域的拓展。
結語
碳纖增強環氧樹脂復合材料在部分高檔汽車及賽車結構件上的成功應用表明,復合材料完全可以替代金屬被用于汽車結構件中。然而,由于材料和設備昂貴,再結合目前汽車生產的工藝鏈和產品鏈,以及材料回收重復利用等問題,目前其綜合考量成本與效益還不具備量產化的條件,導致碳纖增強環氧樹脂復合材料在汽車結構件上的應用具有很大的局限性,這使得鋼材及高強度鋁合金目前仍然是汽車結構件的主流材料。盡管如此,近年來,長纖維增強熱塑性復合材料及其加工技術的快速發展讓人們看到了新的希望。隨著長纖維增強熱塑性復合材料在汽車次承力結構件應用方面的日益成熟,相信人們一定會找到更具成本效益的、同時能滿足使用性能要求的材料解決方案,以實現汽車結構件、特別是主結構件的輕量化。
123,123
另外,還需要強調的是,作為一種完全有別于金屬材料的新型材料,復合材料的汽車零部件設計涉及結構設計、鋪層設計及強度設計等多個方面,它離不開大量的計算和經驗的積累。要實現復合材料汽車零部件的規模化生產,還需要制訂相應的各種標準規范,包括材料的檢驗和測試標準以及生產工藝規范等。在實際的復合材料設計過程中,應根據材料的利弊特性,針對特定的結構形狀、性能和成本要求,在結構設計早期即開始為具體的工藝方案、可能出現的問題以及處理方法等做出盡可能細致的分析和規劃,這是實現高水平復合材料機構的重要前提。因此,開發復合材料汽車部件是一個非常復雜的系統工程。目前,國外很多整車廠已建有完整的復合材料工藝體系和設計體系,相比之下,國內的汽車行業在此方面還是一個空白。隨著復合材料在汽車工業應用的日益增多,建立專業的研發團隊已成為國內汽車整車廠商的當務之急。
123456
來源: 科研轉載