摘要:
碳纖維的高強和脆性使其拉伸試驗過程有別于柔性紡織纖維。為了得到更精確的結(jié)果,本文研究了T300-12K碳纖維單絲拉伸過程中,拉伸速度對測試系統(tǒng)誤差的影響。通過研究系統(tǒng)誤差的角度,分析拉伸速度影響的大小和趨勢。
1 引言
碳纖維的高比強、高比模[1]、耐高溫等優(yōu)良性能使其得到廣泛的應(yīng)用[2]。作為理想的高性能材料,被廣泛應(yīng)用于航空、航天等高科技領(lǐng)域以及化工、電子、冶金、汽車、醫(yī)療和體育等一般工業(yè)領(lǐng)域[3],具有廣泛的發(fā)展前景[4]。作為結(jié)構(gòu)材料應(yīng)用時,碳纖維復(fù)合材料的力學(xué)性能很大程度上依賴于碳纖維的力學(xué)性能[5],因而對碳纖維的伸長率、模量的準確測試是對其評價的一個重要內(nèi)容[6],它涉及碳纖維復(fù)合材料的設(shè)計與使用[7-9]。
在碳纖維的幾個力學(xué)參數(shù)中,纖維的伸長率和模量是很難準確測試的。原因是碳纖維極細(5μm~8μm) ,為脆性、高強低伸纖維。它的伸長率在0.5%~2.0%之間。這就使得拉伸過程的各種因素對結(jié)果極易產(chǎn)生顯著影響。
本文來自123
這些因素有很多,例如拉伸的速度、隔距、測試系統(tǒng)本身的傳感和誤差、固定纖維用的膠水的黏性和固化后的剛度,以及固定紙卡的種類及剛度、環(huán)境的溫濕度、人為操作的誤差等等。
查閱國內(nèi)外大量的關(guān)于碳纖維力學(xué)性能測試的文章,發(fā)現(xiàn)測試過程中的拉伸速度對碳纖維模量測試方面僅有少量研究,未能找到拉伸速度對結(jié)果的影響具體有多大,從而對測試數(shù)據(jù)進行修正。
本文主要研究的是不同的拉伸速度對系統(tǒng)誤差具體產(chǎn)生多少影響,從而對伸長率、模量等測試結(jié)果進行修正,并提出更為適合碳纖維的拉伸速度。
為了研究方便,假設(shè)碳纖維的拉伸變形和系統(tǒng)受力產(chǎn)生的伸長都是彈性形變。利用線性回歸的數(shù)學(xué)方法,找到當(dāng)隔距為零時,不同拉伸速度下,所產(chǎn)生的伸長量。這個伸長量,就是系統(tǒng)誤差所產(chǎn)生的,進而可以計算出測試過程的系統(tǒng)誤差的影響大小,單位是mm/cN,又可稱為系統(tǒng)軟度。根據(jù)這個數(shù)值就可以修正測試數(shù)據(jù)了。
內(nèi)容來自123456
2 碳纖維單絲強伸試驗
2.1 試驗樣品
試驗采用市售商品日本東麗公司聚丙烯腈( PAN) 基碳纖維,牌號 T300B-12K,簡稱 T300,它是國際公認的通用級標準碳纖維,性能參數(shù)見表1。
2.2 儀器與設(shè)備
試驗采用上海新纖儀器有限公司的XQ-1A型單纖維拉伸試驗機。
2.3 制樣
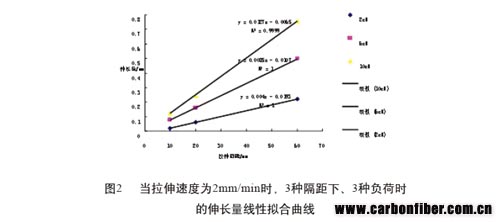
碳纖維單絲的強伸試驗不同于其他柔性纖維的單纖維試驗。碳纖維不能直接夾持在預(yù)定隔距的兩夾頭間。其原因很簡單,一是纖維的脆性使整個夾持成功率極低,纖維往往在夾持過程中因彎折而斷裂。二是即使夾持成功,夾持端會對纖維產(chǎn)生損傷,使纖維的斷裂發(fā)生在鉗口處,所測數(shù)據(jù)不能反映纖維的真實特性。因此,碳纖維單絲的強伸試驗首先要求將單根碳纖維粘貼于特制的試樣卡上,
123456
如圖1所示 。之后再用顯微鏡逐根觀察確定所固定的纖維是否是碳纖維。
2.4 試驗方案
設(shè)定4個不同的拉伸速度,2mm/min、4mm/min、10mm/min、20mm/min。在每種拉伸速度下用3個不同的隔距10mm、20mm、60mm進行拉伸試驗。每個拉伸速度每個隔距測量的樣品數(shù)量至少為30根纖維。
3 結(jié)果與分析
根據(jù)對482根成功拉伸的碳纖維分析其拉伸曲線,計算得出表2數(shù)據(jù)。
從表2可以看出,同一拉伸隔距下拉伸速度越快,測試得出的模量越大。這與我們從理論上的判斷和其他學(xué)者的研究是一致的,且拉伸速度越快,不同隔距下測得的模量差異也更明顯。
為了計算出不同拉伸速度產(chǎn)生的系統(tǒng)誤差,在每一根纖維拉伸的數(shù)據(jù)中,分別找出當(dāng)拉伸負荷為2cN、6cN和10cN時測試得出的伸長量,然后對照相應(yīng)的拉伸速度和隔距,找到當(dāng)拉伸隔距為零時系統(tǒng)產(chǎn)生的伸長量。
本文來自123
從圖2可以看出,在拉伸速度為2mm/min下,拉伸負荷分別達到2cN、6cN、10cN時,拉伸隔距和測試結(jié)果的伸長量為線性關(guān)系。
從圖3可以看出,拉伸速度在2mm/min下,找到當(dāng)拉伸隔距為零時的系統(tǒng)所產(chǎn)生的伸長量??梢钥闯霎?dāng)拉伸隔距為零時,系統(tǒng)隨著受力的增大,伸長量也是在逐漸增大的,而且也呈線性關(guān)系。
從圖2和圖3可以發(fā)現(xiàn),碳纖維的強伸過程和系統(tǒng)受力伸長的過程都沒有發(fā)生緩彈性的形變,屬于彈性形變,證明了前言部分纖維變性和測試系統(tǒng)變形是彈性變形的假設(shè)是成立的。
其中當(dāng)拉伸負荷為2cN、6cN、10cN時,伸長量為負值。從表面上看,似乎有悖于常理,但從拉伸儀器的傳動和靈敏裝置的設(shè)計角度,也不是不能解釋,但仍有待進一步的研究。由于這不是本文的重點,就不在此多言。
123456
從圖4我們同樣得到了和圖2一致的結(jié)論,拉伸的隔距和測試讀出的伸長量為線性關(guān)系。圖5的結(jié)果有點出乎意料,似乎與預(yù)期的差異較遠,無法完成線性回歸。至于原因還有待進一步研究和分析。
圖6和圖7的結(jié)論與圖2和圖3一致,這里就不贅述了。
圖7 的擬合曲線幾乎經(jīng)過0—0點,這一點與理論上的狀態(tài)更加接近。
圖8和圖9的結(jié)論與之前的圖2和圖3基本一致。圖9的線性回歸方程的R 2值為0.86,接近0.9,屬于近似線性回歸。但由于之前圖3、圖7的結(jié)論和考慮到纖維本身的弱節(jié)分布不勻等因素,還是基本可以判斷應(yīng)該是線性關(guān)系的。
內(nèi)容來自123456
根據(jù)圖3、圖7和圖9,得出,當(dāng)拉伸速度為2mm/min、10mm/min、20mm/min下,系統(tǒng)受力而產(chǎn)生的伸長。如圖10所示。
同時我們可以看到,系統(tǒng)誤差產(chǎn)生的伸長量與拉伸速度也是呈線性關(guān)系,而且是正比例關(guān)系。
從圖10我們還看到一個有待研究的問題,當(dāng)拉伸速度小于10mm/min時,系統(tǒng)伸長為負值,這樣的倒伸長量是如何產(chǎn)生的,仍有待進一步的研究。
最后可以根據(jù)線性回歸后的分析結(jié)果,對測試讀出的數(shù)據(jù)進行修正。將系統(tǒng)受力產(chǎn)生的伸長量剔除,得到碳纖維真正的伸長率和模量等力學(xué)指標,見表3。
4 結(jié)論
試驗結(jié)果證明了碳纖維的伸長和測試系統(tǒng)受力產(chǎn)生的伸長都為彈性伸長,沒有發(fā)生緩彈性變形。隨著拉伸速度的增加,系統(tǒng)誤差也增加,而且呈線性關(guān)系。測試碳纖維時,可盡量使用10mm/min附近的速度拉伸,太慢或者太快,都容易增大系統(tǒng)誤差。對測試結(jié)果造成影響。
123,123
參考文獻:
[1] J. W . Johnson . Factors affecting the tensile strength of carbon-graphite fibers[J] . Journal of applied polymer symposia, 1969, (9):229~243 .
[2] D . J . Thorne . Distribution of internal flaws in acrylic fibers [J] . Journal of applied polymer science, 1970, (14):103-113.
[3] 姚江薇,于偉東.碳纖維單絲強伸試驗的影響因素
[J].材料科學(xué)與工程學(xué)報,2005.98(6):810-813.
[4] T . Tetsuy, M . Takashi . Size effect on tensile strength of carbon fibers [J] . Materials science and engineering, 1997, A238:336-342.
[5] K . L . Pickering, T . L . Murray. Weak link scaling anlysis of high-strength carbon fiber [J] . Composite: Part A, 1999,30:1017-1021.
[6] 張為芹,田艷紅.高強碳纖維束絲拉伸性能測試影響因素的研究
[J].理化檢驗-物理分冊,2006.42(11):541-553.
[7] 潘慧銘,黃素娟.表面、界面的作用于粘接機理[J] . 粘接,2003,24(3):41-46.
123,123
[8] 于偉東 . 纖維弱節(jié)的力學(xué)特征與判定[J] . 東華大學(xué)學(xué)報, 2003, 29(2):32-36.
[9] 董立民, 夏源明, 楊報昌. 纖維束的沖擊拉伸試驗研究
[J]. 復(fù)合材料學(xué)報, 1990, 7(4):9-15.
中國纖檢雜志